Though Maxim data sheets generally recommend 10-mil trace width and 10-mil spacing between traces, 5-mil traces and 5-mil spacing have been demonstrated to give equivalent results, but with higher series resistance. Because the measurement errors induced by the higher series resistance are predictable with Maxim temperature sensors and can be compensated, 5-mil traces and spacing may be used with good results.
The desire for narrower interconnects between sensors thermal diodes is a direct result of the trend of making complex printed circuit boards as small as possible. The data sheets for most remote-diode temperature sensors recommend interconnect lines between the sensor and the thermal diode a maximum of a few inches long with 10-mil width/10-mil spacing. Longer and narrower traces may be used, provided that their effects are understood.
Changing the length and width of the circuit board traces can change the amount of series resistance and noise pickup associated with those traces. Understanding these effects, an informed decision can be made as to whether longer and narrower traces are acceptable.
Series Resistance
Increasing the length of the thermal diode traces (DXN and DXP) or decreasing their width increases the series resistance, which results in addiTIonal error in temperature readings from the remote sensor (Figure 1). Most of Maxim's remote sensors exhibit measurement error of approximately 0.45°C/Ω of series resistance.ΔT = ΔRs x 0.45°C
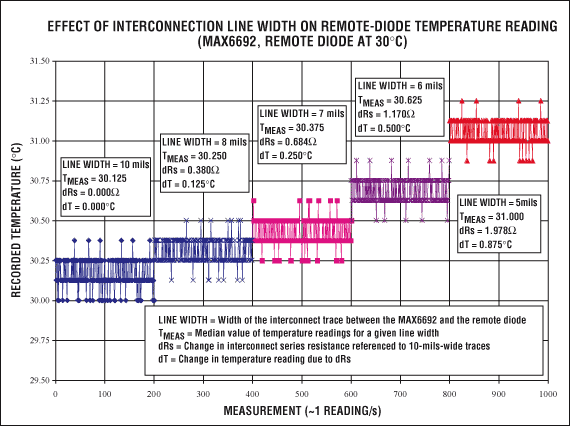
Figure 1. The effect of DXN-DXP line width on temperature measurement is shown. Smaller line widths have higher series resistance and, therefore, increase the measured temperature by 0.45°C/Ω.
Temperature sensors manufactured by other manufacturers someTImes use higher values of diode bias current, which produces larger errors due to series resistance. In applications with known interconnect series resistance, the error can be corrected by making proper adjustment to the temperature reported by the sensor.
In the experimental board fabricated for this study, we made interconnects 10in (25cm) long with line width/spacing ranging from 5 mils to 10 mils. The series resistance of different line width varies from ~2Ω to ~4Ω, and the 5-mil traces have about 2Ω more series resistance than the 10-mil traces. The temperature readings using the 5-mil traces are roughly 0.9°C higher, as expected. Series resistance is proportional to trace length, so the effect of different trace lengths can be easily calculated.
Because the measurement errors induced by the higher series resistance are predictable and Maxim temperature sensors can be compensated, 5-mil traces and spacing may be used with good results (Figure 2).
Maxim has a range of temperature sensors that includes a series resistance cancellation function, which eliminates the effect of series resistance automatically as part of the measurement process. Examples of temperature sensors with series resistance cancellation are the MAX6654, MAX6690, MAX6601, MAX6697, and MAX6698.
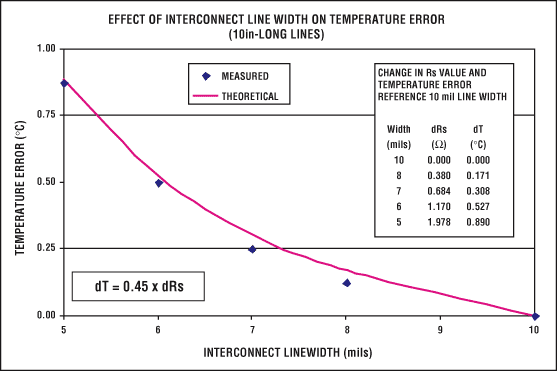
Figure 2. Measured and theoretical temperature errors caused by series resistance are compared. Temperature reading with 10-mil line width/spacing is used as reference.
Noise Pickup
Maxim's temperature sensors have very effective noise rejection, as shown in the typical operating curves in all remote-sensor data sheets. These curves show the effect of high levels of noise inserted on the sense traces. In addition, the use of a 2200pF capacitor connected between DXN and DXP helps to significantly reduce the amplitude of any noise pickup.To obtain best results when connecting the temperature sensor to the thermal diode, follow these simple guidelines:
- Run a GND trace on each side of the DXN and DXP signal traces.
- Avoid routing high-speed signal traces close to the DXN and DXP traces.
- When the traces must cross, be sure they cross at right angles.
- Insert a ground layer between the high-speed signals and DXN/DXP traces.
- Whenever possible, run a GND trace on each side of the high-speed signal traces.
Conclusion
Based on the results presented in this application note, good results can be obtained when using PC board traces that are narrower than generally recommended in data sheets for remote-diode temperature sensors.